Barcode Tracking While Using QuickBooks in a Manufacturing Operation
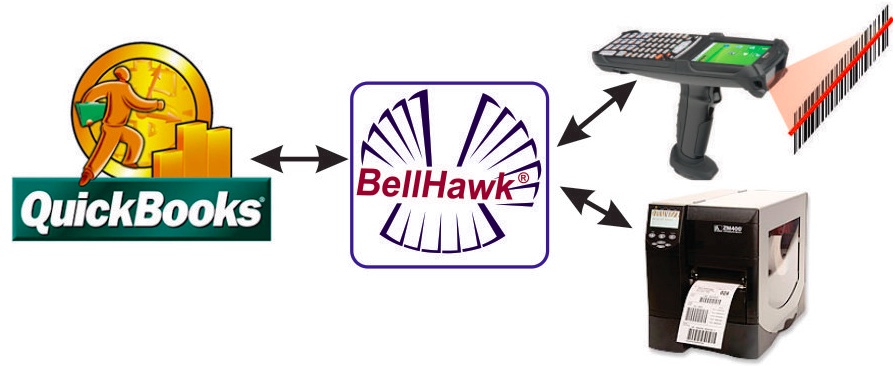
The primary problems are:
1. QuickBooks representation of inventory is a table of items that gives the total quantity on hand at all locations in the whole business. Manufacturers need to track their raw, work-in-process and finished goods inventory by the location of the material and more-importantly, by the containers these materials are in. These containers many be bins, boxes, barrels, totes, pallets and even rolls and reels of material.
In a manufacturing business these containers move around during the manufacturing process. Also materials are taken from containers as part of the manufacturing process and resultant products and work-in-process are placed into containers. To track these containers we need to attach a unique “license-plate” tracking barcode on each container as well as attaching a unique location barcode on or near each rack, shelf, and floor location. Then material handlers can scan the tracking barcode on the container and the location barcode near to where it is moved, in order to track the movement of each container.
2. QuickBooks’ view of manufacturing jobs is either simple one-step assembly of purchased parts into a finished product or a work-order on which people record labor hours. Neither is an adequate representation of what goes on in most manufacturing businesses.
In a manufacturing business, materials are consumed and produced in a series of operations that transform raw materials into work-in-process and then eventually into finished goods. So we need a system that knows how to represent routes of operations with each operation having a bill-of-materials to be consumed on that operation, as well as tracking labor and machine time consumed on the operation, and multiple materials and possibly scrap produced by each operation.
Because it does not have these underlying data structures in its database, QuickBooks cannot produce barcoded travelers which are essential to the tracking of the consumption of materials and labor and machine time on operations. And because it does not understand about containers it is not able to use barcode scanning to record the use of materials on manufacturing operations or their production by operations.
3. QuickBooks has no notions of shipments. All it knows about are invoices. As a result it cannot generate barcoded picking sheets for finished goods and cannot use wireless mobile computers with integral barcode scanners to record the picking, packing and shipping of finished goods.
Also QuickBooks cannot generate packing slips or bills of lading for shipments, nor can it print barcode labels to attach to each pallet or other container shipped to the customer.
Does this mean that QuickBooks cannot be used in a manufacturing enterprise? To the contrary, QuickBooks is very appropriate as long as it is paired with a barcode tracking system, such as BellHawk®, which is designed for use in a manufacturing environment and which will handle all the barcode inventory and work-in-process tracking functions.
The resultant combination then has capabilities that can exceed those of ERP systems costing an order of magnitude more. Also the resultant combination is simpler to use with a much lower total cost of ownership.
Does this mean that QuickBooks cannot be used in a manufacturing enterprise? To the contrary, QuickBooks is very appropriate as long as it is paired with a barcode tracking system, such as BellHawk®, which is designed for use in a manufacturing environment and which will handle all the barcode inventory and work-in-process tracking functions.
The resultant combination then has capabilities that can exceed those of ERP systems costing an order of magnitude more. Also the resultant combination is simpler to use with a much lower total cost of ownership.
For more details on how to solve these issues, please download the white paper “Adding Barcode Tracking to QuickBooks for Manufacturers”, by Dr. Peter Green which is downloadable as a PDF from www.BellHawk.com under the White Papers tab.
Follow us on Facebook: http://www.facebook.com/theBarCodeNews
Follow us on Twitter: http://www.Twitter.com/theBarCodeNews